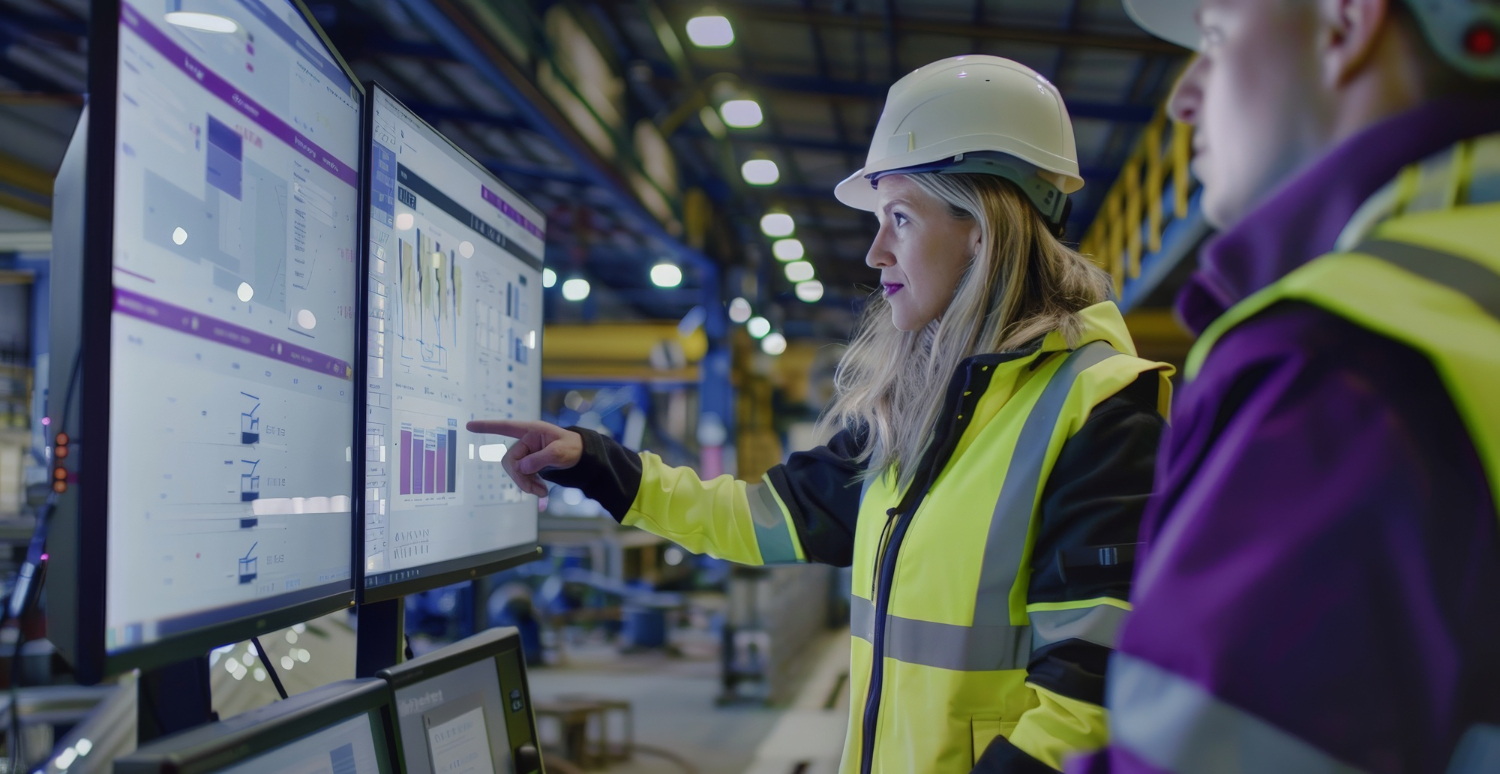
Most businesses struggle with equipment-related challenges that silently drain profits and productivity. Missing assets, unexpected breakdowns, and chaotic maintenance schedules aren’t just annoyances—they’re serious obstacles affecting your bottom line.
Modern equipment management software offers a solution to these persistent challenges. Companies implementing strategic equipment management report impressive results: up to 40% less equipment downtime and 25% longer asset lifespans—directly boosting operational efficiency and cutting costs.
The Evolution of Equipment Management: From Clipboards to Digital Solutions
Traditional Equipment Management Pitfalls
For decades, businesses tracked equipment using archaic methods—clipboards, disorganised spreadsheets, and the mental notes of veteran employees. Equipment would vanish, maintenance records would be scattered across documents, leading to premature failures, and managers would lack real-time visibility into equipment status.
These problems cost far more than immediate expenses suggest. Equipment failures trigger missed deadlines, production delays, and frustrated customers.
The Shift to Digital Equipment Tracking Systems
Digital equipment tracking represents a fundamental change in how businesses view physical assets. Rather than seeing equipment as necessary expenses, organisations now recognise these items as investments requiring careful management throughout their useful lives.
Digital systems provide instant access to location data, usage metrics, maintenance histories, and performance statistics—all available from any connected device.
Key Capabilities of Modern Equipment Management Software
Today’s equipment management software provides real-time tracking using RFID, GPS, or QR technology, letting managers locate any piece of equipment instantly. Automated maintenance scheduling based on actual usage patterns prevents unexpected breakdowns. Comprehensive equipment histories document every repair and performance issue, creating valuable institutional knowledge.
Mobile functionality allows field teams to update information on the spot, while integration with existing business systems creates a unified data environment that drives smarter equipment investments.
Core Components of Effective Equipment Management Systems
Strong equipment management systems combine several essential elements:
Real-time Equipment Tracking and Location Monitoring
Modern tracking technologies save countless hours previously wasted searching for equipment. They also create accountability for asset movement between locations or departments, reducing losses and unauthorised use.
Preventive Maintenance Scheduling Capabilities
Instead of waiting for breakdowns, smart systems anticipate needs based on manufacturer recommendations, actual usage hours, and performance data indicating potential issues. This proactive stance keeps operations running smoothly by minimising surprise failures and extends equipment lifespan by addressing small problems before they become major repairs.
Equipment Utilization Analytics
Usage data reveals which assets sit idle most of the time and which ones might need backup resources to prevent burnout. These insights help businesses maximise return on equipment investments by ensuring assets work at optimal capacity.
Inventory Management and Procurement Integration
Comprehensive equipment inventory management connects asset tracking with procurement. Systems can automatically reorder consumables and replacement parts when supplies run low, while historical usage data helps forecast future equipment needs more accurately.
Implementing Maintenance Scheduling for Maximum Uptime
Moving from Reactive to Preventive Maintenance
The transition from reactive (fix-when-broken) to preventive maintenance represents one of the most significant efficiency improvements for equipment-dependent operations. Maintenance scheduling software enables this shift by:
- Establishing regular service intervals based on manufacturer recommendations
- Creating maintenance protocols for each equipment type
- Tracking completed maintenance activities against schedules
- Documenting maintenance procedures for consistent execution
Organisations that successfully implement preventive maintenance programs report 30-40% reductions in equipment downtime and 10-20% extended asset lifespans.
Creating Effective Maintenance Schedules Based on Usage Data
One-size-fits-all maintenance schedules rarely provide optimal results. Modern systems allow for dynamic scheduling based on:
- Actual equipment usage rather than calendar intervals
- Operating environment conditions that impact wear rates
- Historical performance data identifying potential failure patterns
- Criticality of equipment to operational continuity
These data-driven schedules ensure maintenance resources focus on equipment that truly needs attention while avoiding unnecessary servicing of rarely-used assets.
Automating Maintenance Notifications and Work Orders
Automation eliminates manual coordination of maintenance activities:
- Generating work orders when maintenance thresholds are reached
- Assigning tasks to appropriate maintenance personnel
- Sending notifications to equipment users about upcoming service
- Escalating alerts for overdue maintenance on critical equipment
This automation ensures maintenance activities occur as scheduled without constant manual oversight, improving compliance rates and resource utilisation.
Tracking Maintenance History for Better Decision-Making
Comprehensive maintenance histories provide valuable insights:
- Identifying recurring issues that may indicate deeper problems
- Calculating true maintenance costs for each asset
- Evaluating maintenance technician performance and efficiency
- Supporting warranty claims with documented service records
These historical records transform maintenance from a cost center to a strategic function that directly impacts operational efficiency and equipment ROI.
Optimising the Equipment Lifecycle with Data-Driven Strategies
Equipment Acquisition and Onboarding Best Practices
Effective asset lifecycle management begins before equipment arrives. Smart organisations standardise equipment specifications whenever possible, evaluate total ownership costs beyond purchase price, and digitise technical documentation immediately.
Utilisation Monitoring and Performance Benchmarking
Tracking actual versus expected output reveals whether the equipment meets productivity targets. Comparing performance across similar units identifies outliers needing attention, while precise operating costs calculated per hour support better deployment decisions.
Predictive Maintenance for Extended Equipment Lifespan
Predictive approaches analyse performance data to anticipate failures before they occur. Systems monitor deviations from normal operating parameters, analyse vibration patterns or temperature changes indicating potential issues, and schedule targeted interventions before critical failures happen.
End-of-Life Planning and Replacement Optimization
Performance metrics and maintenance histories determine optimal replacement timing before reliability problems impact operations. Complete cost data supports repair-or-replace decisions as equipment ages, while technology upgrade planning ensures new equipment enhances operational capabilities.
Practical Implementation: A Step-by-Step Approach
Auditing Current Equipment Management Processes
Before implementing new systems, thoroughly assess existing practices:
- Document current tracking and maintenance procedures
- Identify pain points and efficiency gaps
- Quantify costs of current equipment management challenges
- Establish baseline metrics for measuring improvement
This assessment provides critical context for system selection and implementation planning.
Selecting the Right Equipment Management Solution
With numerous operational efficiency tools available, selection criteria should include:
- Required functionality based on business needs
- Scalability to accommodate future growth
- Integration capabilities with existing systems
- Mobile accessibility for field personnel
- Ease of use for all stakeholders
- Implementation and ongoing support resources
- Total cost of ownership over a 3-5 year period
Focus on solutions that address your specific equipment management challenges rather than pursuing unnecessary features.
Data Migration and System Integration Strategies
Successful implementations require thoughtful data handling:
- Auditing existing equipment data for completeness and accuracy
- Prioritising critical information for initial migration
- Establishing data standards for consistent recording
- Creating integration points with related business systems
- Validating data integrity after migration
Proper data management ensures that the new system delivers value from day one.
Training and Adoption Ideal Practices
Technology implementations succeed or fail based on user adoption:
- Providing role-specific training for different user groups
- Creating quick-reference guides for common tasks
- Identifying and supporting internal champions
- Establishing clear expectations for system usage
- Collecting and addressing user feedback
Investing in proper training typically yields 3-4x returns through improved system utilisation.
Measuring Success: KPIs for Equipment Management Efficiency
Establish clear metrics to evaluate implementation success:
- Reduction in unplanned equipment downtime
- Maintenance compliance rates
- Equipment utilisation improvements
- Time saved in equipment location and deployment
- Extended equipment lifespan
- Reduction in rush repair/replacement orders
- Overall maintenance cost per equipment hour
Regular review of these metrics guides ongoing optimisation efforts.
Case Studies in Equipment Management Transformation
Construction Company Reduces Equipment Downtime by 37%
A mid-sized construction firm implemented comprehensive equipment tracking throughout their operations. Equipment downtime dropped 37%, rental replacement costs fell by $213,000 annually, and project delivery timelines improved by 22%. Most impressively, they reached a complete return on investment within nine months.
Healthcare Facility Extends Equipment Lifespan While Ensuring Compliance
A regional healthcare network integrated maintenance scheduling software with their existing clinical systems. Medical equipment lifespans were extended by an average of 3.2 years, regulatory maintenance compliance reached 100%, and maintenance technician overtime dropped 42%.
Manufacturing Operation Streamlines Maintenance Scheduling Across Multiple Sites
A manufacturing enterprise standardised maintenance protocols across eight facilities, decreased parts inventory by 31%, reduced mean time to repair by 47%, and improved overall equipment effectiveness by 23% through consistent maintenance practices.
Event Management Company Optimizes Inventory and Logistics
An event management firm deployed equipment inventory management to track its extensive AV equipment. The system eliminated the double-booking of critical equipment, decreased loading time by 62%, and reduced lost equipment costs by 91%.
Equipment Management as a Competitive Edge
Streamlined equipment management delivers measurable advantages that directly impact operational results. When preventive and predictive maintenance replaces reactive approaches, unexpected equipment downtime decreases significantly. Properly maintained capital assets last longer, delaying expensive replacement purchases and improving return on investment.
As you consider improving your equipment management approach, start with a thorough assessment of current pain points and clear objectives. Select solutions that address your specific challenges rather than chasing unnecessary features.
Equipment often represents one of the largest capital investments for businesses across industries. Strategically managing these assets transforms them from necessary expenses into powerful tools driving business growth, productivity, and competitive advantage.